Among all the different types of fuel cells (such as direct methanol fuel cells, solid oxide fuel cells), multi-stack cell arranged proton exchange membrane fuel cells (PEMFC) have been successfully commercialized due to their excellent performance. PEMFC is considered as one of the ideal power sources to meet the future energy and environmental requirements because of its high energy conversion efficiency, low emission and high energy and power density. Of all the components in the PEMFC system, the stack of hundreds of bipolar plates and membrane electrodes accounts for 60% of the cost of the battery system and 30% of the cost of the vehicle. The bipolar plate is one of the two key structural components in the PEMFC stack, which is called the "skeleton" of the fuel cell stack, and determines the core indicators of the battery such as weight, volume and cost to a large extent. The metal bipolar plate has the advantages of higher strength, good formability, strong impact resistance, high power density, thin thickness, low hot melt, low cost, low gas permeability, excellent electrical and thermal conductivity, good machinability, high density, high strength, good gas resistance, etc., which can provide good power density and low temperature (-40℃) start-up guarantee for passenger cars. And suitable for high volume and low cost production.
By applying the roll forming technology mastered by the team, the common problems of the formed parts of the two processes can be avoided, such as the redundant deformation of the roll forming, the deformation section can not be formed (limited by the roller has only one fixed degree of freedom), and the large load of the stamping forming, the mold wear is serious, and the material is easy to crack, so as to greatly improve the performance of PEMFC.
In addition to the metal bipolar plate, the current lithium battery energy density has basically reached the limit level of the industry, which puts forward higher requirements for the lightweight of the battery pack structural parts. The lightweight of battery pack structural components is mainly achieved through the application of high-strength lightweight materials, lightweight structural design and advanced manufacturing processes. At present, the process of making battery packs by manufacturers on the market, such as die casting, has drawing depth, insufficient vibration and impact strength of battery packs, and there will be many product defects such as cracks, rebound and other problems. The team is applying roll punching technology to the design and manufacture of lithium battery packs, which can effectively avoid several common problems of process forming parts, such as cracking, wing fold, etc., thus greatly improving the performance of battery packs.
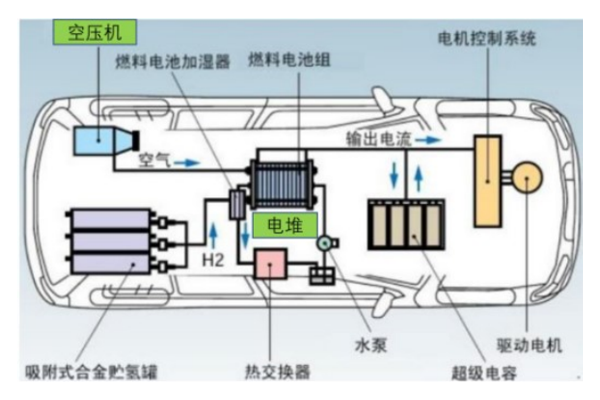
氢燃料电池系统的PEMFC电池堆

辊压工艺双极板成型
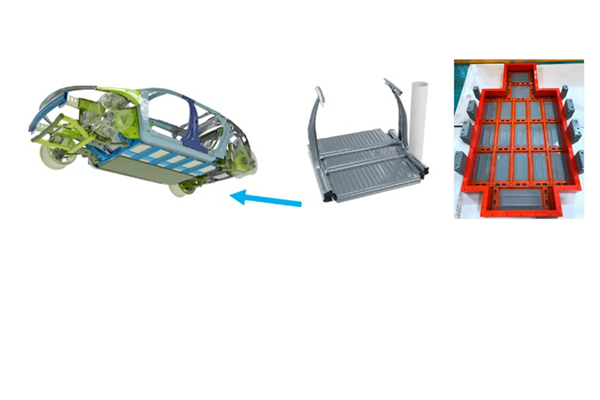